Door Structure and Technological Features
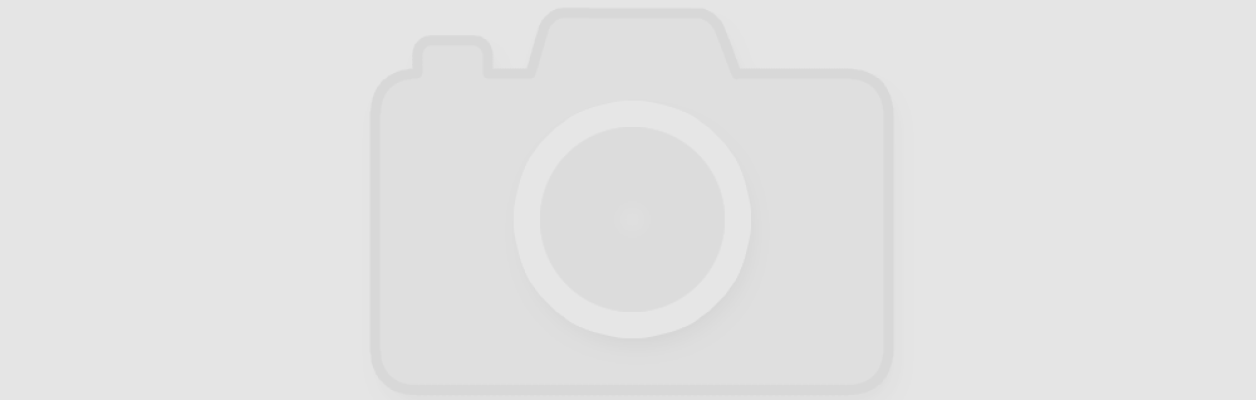
We made doors of so called combined mass i.e. laminated solid pine and MDF sheet coated with valuable and exotic woods veneer and decorated with polyurethane lacquer or paint from ITALCOLOR (ICA) Italy.
05.10.2011
We made doors of so called combined mass i.e. laminated solid pine and MDF sheet coated with valuable and exotic woods veneer and decorated with polyurethane lacquer or paint from ITALCOLOR (ICA) Italy.
While choosing the structure and the production technique we minded that although doors made of natural wood mass have high application performance at the same time they have certain disadvantages:
- natural defects (such as knots, cracks and pitch pockets etc.)
- hygroscopicity (ability to lose moisture or absorb water steams depending on air humidity and temperature)
- solid door panels may alter in size under sharp changes of humidity level even in dry rooms, this leads to worse appearance, parts of panels without paint along the draft fillets, worse vendibility after adzing, adjusting or partial repainting when panels start to grind in the box.
These problems appear due to inadequacy of the micro climate in the room (high air dryness or humidity, no air conditioning) to proper conditions of door usage, rather than low door quality.
The second basic problem of solid doors is how well and correctly the timber was dried. Modern complex drying chambers are necessary for correct timber drying; they have gradual “soft” process of drying, which results in proper humidity level (8-10%) and no internal pressure.
Are there many domestic manufacturers that can afford drying appliances for veneer and interior doors? In most cases the timber is dried in small rooms with electric tens, fans or gas torches, these appliances can remove only humidity but internal pressure remains together with uneven drying.
Given the abovementioned the application of the substitutes of natural wood in door technologies gives both cheaper products and fewer defects proper to natural timber and also creates wider opportunities for designers.
First of all it concerns such sheet material as MDF which has high hydrophobic property, high density and is ecologically clean.
MDF (Medium-density fiberboard) is one of the most up-to-dated technological achievements of woodworking industry. Fibrous plates of even density are made of woods for logging and wastes (chips) of woodworking. They are grinded to small blocks (chips) and undergo high-pressure steam processing, then they are grinded to dust in grater and after that under high pressure sheets of 2-38 mm are formed and agglutinated. Agglutination is based on synthetic pitches without formaldehyde. All MDF plates used for door production meet E-1 hygiene class as well as all European standards. The plate surface is even, homogeneous and smooth. MDF resistibility may compete with hardwood.
Application of this material for door production gives high resistance to moisture absorption, firmness and resistibility to blows. MDF is a hard material and is bladed with a special diamond dusted tool; after this the material is painted perfectly.
As for internal filling we made it of combined re-glued solid from agglutination under pressure bars of dried timber without knots. This is the most up-to-dated technique. Thus the bars have different direction of fibers in every layer. This technique helps to avoid deformation.
Hollow panels (cellular filling) and panels with particle board filling can not compete with combined solid doors in heat and sound isolation, and door accessories (loops, locks) are fixed less reliably than in wood.
Given the abovementioned we coat agglutinated bars for leg and cross-section elements of the panel with sheet MDF of 3 mm.
Paneled parts of door cloths, platbands, plug-in quarters with sealant and expanders of boxes are made of MDF of 12-16 mm.
To bars agglutination and veneer application we use glue “Rhenocol Propellerleim” (Super W/DW), of DIN EN 204/D3 quality class. It is checked up on WATT 91 for high breaking strength (more than 7 H/sq m at 80° C).
We use hi-tech equipment to manufacture doors. Agglutinated bars are coated with sheet MDF in a special hydraulic press and veneered in a hot vacuum-membrane press.
Exterior door dressing
We use beech, oak and ash-tree veneer of high quality as well as 15 exotic trees like sweet cherry, nut, venge, mahogany, zebrano and ebony etc to coat the doors.
Natural veneer dressing has some distinctive features. E.g. various parts of veneer on the door surface may differ slightly in color depending on the angle of light reflection and impossibility of choosing completely identical veneer on the first stages. The final color is seen only after the lacquering and so tones of the paint may vary even in the same item. But this uneven color of the surface makes the doors unusual, gives natural charm and proves that you have doors made of natural material.
Accessories
We use only qualitative Italian accessories that guarantee long and reliable operation.
Door loops on bearings provide reliable fastening of door panel (color scheme includes mat nickel, bright chrome, bright brass (gold) and mat brass).
Door mechanisms and locks are from “AGB” (color scheme includes brass (gold), bright chrome and mat chrome).
Additional information
- Any door model we make can be sliding that provides wider opportunities for interior designers to transform rooms and solves the problem of “narrow spaces” in flats and offices.
- Doors are made according to standard sizes: 600 mm, 700 mm and 800 mm. the height is 2000 mm and width 40 mm.
- Doors can also be made according to non-standard sizes and any complexity and furnishing.
- Each door is completed with box with sealant, accessories (loops, lock) and glass.
- The box is designed to keep the fixture (anchor bolts used at installation) unseen in order not to spoil the general view.
- Additional furnishing includes platbands, expanders of boxes and thresholds.
- We also make decorative coats for armoured doors of MDF coated with fine wood veneer and polyurethane varnish.